Silk Manufacturing in Sudbury
Sudbury is a major silk manufacturing centre with four firms producing a wide range of quality fabrics. However, silk manufacture has been established here a mere 200 years or so, whilst textile manufacturing has been established in the town since at least the 14th century. Then it was weaving woollen cloth and the fine medieval timber-framed merchant’s houses in Stour Street were built with the wealth that it created.
When demand for the heavy woollen broadcloth declined in the 16th century the weavers of Sudbury turned to producing lighter fabrics – bays, says, crepes and cotton bunting – in the 18th century much of the bunting was supplied to the Royal Navy for flags.
Origins of the industry in England
Silk making began in China but by the late Middle Ages the knowledge had been brought back to Europe where France and Italy became the leading producers. In 1609 King James I made an effort to stimulate silk making in England by encouraging the planting of mulberry trees, knowing that silkworms fed on the leaves.
Unfortunately his knowledge did not include the fact that it fed on the leaves of the white mulberry, not the black variety which his government was supplying for planting, and the attempt proved abortive.
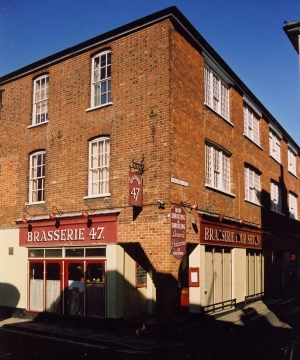
However, by the end of the 17th century another monarch’s religious bigotry succeeded where James’s well meaning efforts had failed. In 1685 the Catholic king of France, Louis XIV, revoked the Edict of Nantes which guaranteed the religious and civic rights of Huguenots – his subjects who followed the Protestant faith. All now had to convert to Catholicism or face persecution. The result was a mass exodus of some 500,000 of his Huguenot subjects into neighbouring countries, taking with them their wealth, arts and skills, including silk weaving. Many came to Spitalfields in London, and so the silk industry was established in England.
Silk comes to Sudbury
Silk weaving came to Sudbury about 100 years later. By then the industry in Spitalfields was well established but plagued by frequent industrial disputes between masters and men, particularly over wages. In 1774 the local magistrates in Spitalfields decided to act and began the first of a series of efforts to regulate the local silk industry, deciding to enforce wage levels on masters and men alike. Many masters then began to move production to country areas within easy reach of London but beyond the interference of the London magistrates. And so silk weaving arrived in towns such as Haverhill, Glemsford and Sudbury. Here there were many skilled textile workers who were happy to work at wages that were higher than they could obtain weaving the traditional fabrics but still only two thirds of what the silk masters would have to pay in Spitalfields.
Weaver’s Cottages
By 1844 there were four silk manufacturers and some 600 silk looms in Sudbury although about half the looms were idle ‘in consequence of the general depression of that year.’ More silk manufacturers arrived in the following years but it must be remembered that silk weaving was still a hand process which could be carried out within the domestic system. This explains the long terraces of three storey weavers’ cottages which are still such an interesting feature of the townscape. Many rows were demolished in the 1960s and 70s but good examples can still be seen in Melford Road, New Street, East Street, Station Road and Cross Street. The ground floor was living space, the top floor for sleeping but the middle floor was ‘the shop,’ a large undivided working area with large windows front and back to admit maximum light. In the centre of the room silk thread was hand wound onto swan’s quills or paper tubes which were inserted into shuttles. The women usually did this task whilst the men operated the loom. The loom was set up at right angles to the window so the light fell across the warp. Given this arrangement, it was not uncommon to see windows on the shop floor with missing panes of glass where a fly shuttle had flown off the loom through the window and landed in the street below! In poor light the weaver would light the oil lamp which hung from the loom beam – most cottages had neither gas nor electricity.
The system had many advantages, not least a feeling of independence and the freedom, particularly for a woman to combine winding with other household tasks. However, there was a downside as well. The weaver was totally dependent on his employer who supplied the warp and skeins of weft yarn and then paid for the finished roll of cloth. The employer might dock his wages if he found imperfections in the weaving. Employment might dry up altogether if there was a recession in the industry and even if work was plentiful the weaver might have to wait to be paid until the roll was finished although he might negotiate some payments on account. Perhaps it was not surprising that local handloom weavers had a reputation for ‘going on the beer’ when they did have money in their pockets!
Development of ‘Manufactories’
The employer also had his difficulties with the system. It was difficult to train new weavers and to ensure the quality of the finished fabric. Some employers therefore centralised production in a building where they could provide training and supervise work on the looms. This trend accelerated with the introduction of wider hand looms and the Jacquard loom for weaving intricate velvets and damasks; both types of loom were too big to fit into a weaver’s cottage.
Nineteenth century documents refer to silk ‘manufactories’ in the town. Some of these were no more than residential houses which were used as warehouses. The weavers only went there to collect their raw materials and to return the finished roll of cloth. A good example is 49A North Street . Other ‘manufactories’ were large work shops with a number of hand looms. Most of these have disappeared although the ground floor of one survives at the back of the former manager’s house at 41 Melford Road.
Two much larger former silk ‘manufactories’ survive which are closer to most people’s idea of a factory, representing attempts to pull together the various stages of production under one roof including silk throwing (spinning), warping, dyeing and weaving.
The oldest of these is 47 Gainsborough Street. Silk weaving was in progress as early as 1791 in the weaving shop now used as a study room on the second floor of Gainsborough’s House next door but the imposing three-storey building at No 47 dates from about 1850. It once had a bank of multi – paned windows on the ground floor in addition to those which survive on the upper two floors facing Weaver’s Lane. In 1851 Mr William Hill lived next door at with a connecting door to his manufactory. In 1851 he employed 200 men, 400 women and 200 girls and installed a factory bell to summon them to work each day.
The other former manufactory is now ‘The Dental Emporium’ which sits on the edge of Acton Square. This two-storey building was built in about 1870 by the firm of Stephen Walters (note the W high up on the end gable) and in turn was occupied by all three of the silk firms which still exist in Sudbury.
Employment in the silk industry reached a peak in the 1850s when about 2,000 silk throwster, dyers and weavers were employed locally. However, a number of firms failed to survive in the decades following the Cobden Free Trade Treaty in 1860; this allowed competition from cheaper French products. The firms that survived this and later recessions in the industry did so by focussing on the quality end of the market and by specialising in a niche market – in the late 19th century a number of firms specialised in silk fabric for parasols and umbrellas.
The Industry today
Today, four silk firms carry on this proud and long history of textile manufacture in Sudbury and we can proudly claim to be the silk capital of England with an estimated 110 metric tons of China silk coming annually into the town. First we have the Gainsborough Silk Weaving Company, founded in 1903 and located on Alexandra Road since 1925. The company produces high quality furnishing fabrics and is frequently approached with special commissions to reproduce historical designs- for example for the restoration of Windsor Castle after the fire They hold the Royal Warrant as Official Supplier of Furnishing Fabric to HM Queen Elizabeth II
Stephen Walters and Company began in Spitalfields in 1720 and moved to Sudbury in the mid 19th century. At their factory in Cornard Road they produce a wide range of fashion fabrics and were commissioned to made silk for the wedding dresses of both the Princess Royal and Princess Diana.
On the same site but with a separate commercial identity is the Humphries Weaving Company Ltd. which moved back to Ashburton Lodge in 2004, after a 30-year spell in Castle Hedingham. It specialises in exclusive, high quality furnishing fabrics, destined for Royal palaces and National Trust properties, together with specially commissioned design work.
Finally there is Vanners Silk which also originated in Spitalfields and made a late move into Suffolk in the 1870s when they opened warehouses in Glemsford (1871) and Haverhill (1874). A merger with Fennell Brothers brought Vanners into Sudbury and their production is now concentrated at their premises in Gregory Street. Much of their output is tie silk produced on computerised looms which have dramatically increased productivity while assuring the highest quality.
This article was written by David Burnett
http://virtualmuseum.sudburysuffolk.co.uk/